Zajmujemy się kompleksowym doradztwem technicznym w zakresie narzędzi skrawających.
Jeżeli szukasz odpowiedzi na swoje pytanie, a nie znalazłeś ich na naszej stronie, prosimy zwróć się do nas !
Zalecenia techniczne dla pił taśmowych
Dla zapewnienia optymalnej wydajności cięcia bimetaliczną piłą taśmową istotne jest dobranie właściwego uzębienia piły w zależności od rodzaju, wielkości i kształtu ciętego materiału. Należy dobrać standardowy kształt zębów o stałej podziałce lub zmienny kształt zębów z podziałką zmienną. Uzębienie zmienne zalecane jest do cięcia materiałów stwarzających problemy związane z nadmierną wibracją.
Zalecane uzębienie piły do cięcia materiałów litych
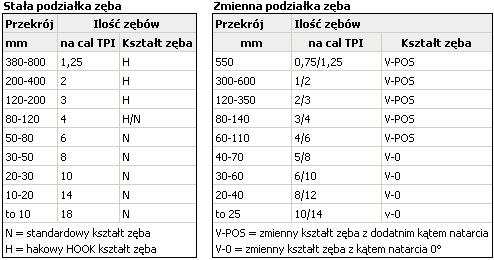
Zalecenia przy cięciu stalowych rur i kształtowników
Przy cięciu stalowych rur i kształtowników decydującą rolę odgrywa prawidłowy dobór uzębienia piły. Najbardziej odpowiednie jest uzębienie zmienne.
Należy również wziąć pod uwagę grubość ścianek, liczbę ciętych elementów, ich ułożenie w pakiecie oraz parametry cięcia.
Instrukcja poprawnego użytkowania
- Brzeszczotom pił taśmowych należy poświęcać taką samą uwagę, jak innym narzędziom. Należy zwrócić szczególną uwagę na:
- - pęknięcia,
- - zakleszczanie się wsteczne brzeszczotu,
- - skręcanie i zmatowienie brzeszczotu.
- Utrzymywać piłę taśmową w dobrym stanie technicznym. Szczególnie należy sprawdzać:
- - czy działa zacisk mocujący oraz mechanizm prostujący,
- - czy występują jednocześnie: ciśnienie hydrauliczne, wystarczająca ilość płynu chłodzącego oraz obroty koła roboczego. jeżeli powyższych brak, wtedy istnieje bezwzględna konieczność regulacji lub wymiany mechanizmu.
- Brzeszczot piły taśmowej założyć na oczyszczone z wiórów koła robocze, ustawić brzeszczot pomiędzy prowadnicami, poprawnie wyregulować naciąg piły oraz ustawić położenie zgarniaczy wiórów.
- Zamocować materiał cięty w uchwycie tak, aby cięcia dokonywała możliwie jak największa ilość zębów (minimalnie 4, a maksymalnie 30).
- W przypadku cięcia pakietu, każdy z jej elementów składowych musi być dobrze zamocowany.
- Przed rozpoczęciem cięcia należy ustalić twardość materiału, wyciąć twarde skazy, wypalić zgorzelinę.
- Przed rozpoczęciem cięcia odlewów należy usunąć z ich powierzchni piasek formierski za pomocą pilnika równiaka lub szczotki stalowej. Piasek może spowodować bardzo szybkie zmatowienie brzeszczotu piły taśmowej.
- Przed rozpoczęciem cięcia konieczne jest zachowanie minimalnego luzu pomiędzy wierzchołkową linią czubków zębów a materiałem ciętym rzędu 10 mm oraz podanie minimalnego posuwu ramienia piły.
- Zwiększać stopniowo posuw ramienia piły. Nie stosować zbyt wysokiego, ani też zbyt niskiego nacisku.
- Podczas cięcia upewnić się, czy następuje ciągły przepływ płynu chłodzącego do przestrzeni cięcia.
- Po przecięciu 2 do 3 detali poprawić prostoliniowość brzeszczotu.
- Sprawdzić czas cięcia detalu. Jeżeli czas ten jest zbyt długi, należy wymienić brzeszczot.
- Nigdy nie ciąć nowym brzeszczotem w starej linii przecięcia. Konieczne jest obrócenie materiału i ponowne uruchomienie cięcia.
Ściernice
Bezpieczeństwo i składowanie
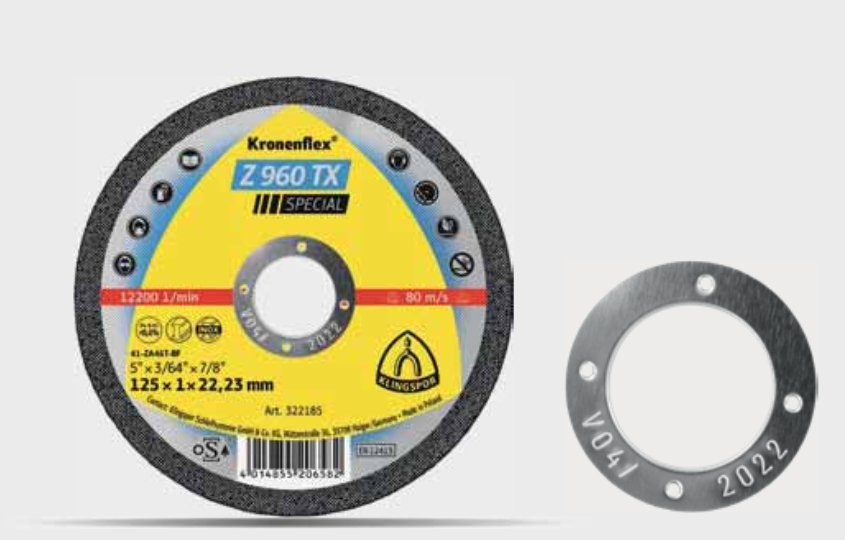
Kwartał | |
---|---|
V 01 | styczeń-marzec |
V 04 | kwiecień-czerwiec |
V 07 | lipiec-wrzesień |
V 10 | październik-grudzień |
Trwałość tarcz do cięcia i szlifowania zależy w pierwszym rzędzie od ich wilgotności. Tarcze do cięcia i szlifowania, narażone po wyprodukowaniu na zwiększoną wilgotność, tracą swą pierwotną trwałość. Przy prawidłowym składowaniu tarcz ich trwałość prawie nie zmienia się przez długie lata. Tarcze do cięcia i szlifowania zagrażają bezpieczeństwu, jeżeli są narażone na bezpośrednie działanie wody lub pary wodnej. Użytkownik tarcz jest zobowiązany do ich stosowania zgodnie z przepisami. Z przyczyn prawnych dotyczy to również daty przydatności tarczy do użytku. Dlatego obowiązuje zasada: Tarcz do cięcia i szlifowania nie wolno stosować po upływie daty przydatności do użytku!
Bezpieczna praca ...
... dzięki staranności i znajomości zagrożeńW czasie użytkowania tarcz do cięcia i szlifowania należy unikać niżej wymienionych zagrożeń:
- kontaktu ciała z wirującą tarczą
- pracy uszkodzoną tarczą
- pyłu szlifierskiego
- wibracji
- hałasu
... dzięki osobistemu wyposażeniu ochronnemu
Należy stosować okulary ochronne, rękawice ochronne, środki ochrony słuchu i maskę przeciwpyłową. W trakcie długotrwałych i trudnych prac szlifierskich należy dodatkowo stosować osłonę twarzy, fartuch skórzany i obuwie ochronne.
... dzięki osłonom ochronnym maszyny
Osłony ochronne dostarczane są razem z maszyną. Nie wolno ich zmieniać ani ściągać. Stosując ściernice garnkowe stożkowe należy całkowicie osłonić powierzchnię zewnętrzną. Ponadto ściernice garnkowe stożkowe mogą być stosowane jedynie w połączeniu z regulowaną osłoną ochronną umożliwiającą zmianę jej położenia w miarę zużywania się tarczy i ograniczenia do minimum możliwości odsłonięcia narzędzia.
... dzięki kontroli wzrokowej i sprawdzeniu przed montażem
Należy upewnić się, że liczba obrotów podana na tarczy jest zgodna z liczbą obrotów maszyny i unikać przekraczania dopuszczalnej liczby obrotów. Należy starannie sprawdzić tarcze do cięcia i szlifowania pod kątem ich ewentualnego uszkodzenia. Nie wolno stosować uszkodzonego narzędzia. Nasze tarcze do cięcia i szlifowania są oznaczone odpowiednimi piktogramami dotyczącymi bezpieczeństwa.
... dzięki właściwemu obchodzeniu się z narzędziem
Należy zwracać uwagę na prawidłowe obchodzenie się z narzędziem. Należy unikać uszkodzenia otworu mocującego lub tarczy w wyniku uderzenia lub upadku... Należy zwracać uwagę na bezpieczne i prawidłowe zamocowanie tarczy i użytkowanie jej z właściwym kołnierzem mocującym.
Przed rozpoczęciem pracy każda tarcza powinna pracować co najmniej przez 30 sekund z prędkością roboczą. Należy przestrzegać wskazówek bezpieczeństwa FEPA.
Optymalna prędkość
Za niska
Jeżeli prędkość stosowanej maszyny jest zbyt niska, tarcze do cięcia i szlifowania mają skłonność do ?nierównomiernego zużywania się krawędzi. Szczególnie przy obróbce materiałów cienkich, jak na przykład w trakcie cięcia blachy lub drutu, ziarna są wyłamywane ze spoiwa i tarcza zużywa się nieproporcjonalnie szybko.
Optymalna
Tarcze do cięcia i szlifowania Klingspor są produktami o wysokiej wydajności i zostały zaprojektowane w taki sposób, aby najlepszą wydajność (liczoną jako stosunek ilości usuniętego materiału do stopnia zużycia tarczy) osiągnąć bezpośrednio przy ich dopuszczalnej maksymalnej prędkości obrotowej. Dlatego też należy w czasie pracy utrzymywać niezmiennie wysoką liczbę obrotów i wybrać ewentualnie maszynę o większej mocy silnika napędowego.
Za wysoka
Maksymalna dopuszczalna liczba obrotów i prędkość obrotowa są nadrukowane na etykiecie każdej tarczy. W interesie własnego bezpieczeństwa należy zwrócić uwagę na to, aby w czasie szlifowania nie przekroczyć podanych wartości.
Właściwa siła nacisku
Istotnym warunkiem osiągnięcia zadowalającego wyniku cięcia jest właściwe dozowanie siły nacisku. Z myślą o oszczędności tarczy popełniany jest często błąd redukowania siły nacisku i wydłużania czasu cięcia. Jeżeli taka praktyka jest stosowana, następuje przegrzanie materiału (zabarwienie na niebiesko), tarcza do cięcia zapycha się i ?spala?. Dlatego też siłę nacisku należy zawsze dobrać na tyle wysoką, aby czas cięcia był jak najkrótszy. Dotyczy to w szczególności materiałów wrażliwych na działanie temperatury o większych grubościach.
Właściwy kąt przyłożenia przy cięciu
Tarcze do cięcia mogą być poddawane jedynie obciążeniom promieniowym. Tylko w ten sposób można uniknąć wybicia, wyłamania i w końcu pęknięcia tarczy, szczególnie przy dużej sile nacisku. Cięty przedmiot należy zamocować w taki sposób, aby tarcza nie miała możliwości obsunięcia się w bok. Ponadto zaleca się, aby obrabiany przedmiot zamocować możliwie jak najbliżej miejsca cięcia, aby nie doszło do wibracji i zejścia z linii cięcia.
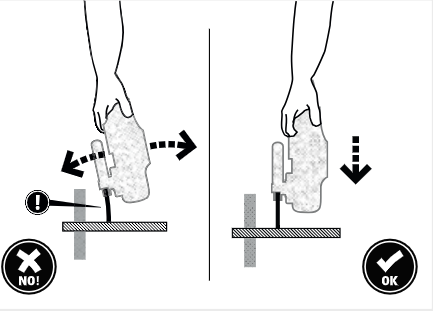
Właściwa twardość
...tarcz do cięcia
Generalnie przy wyborze prawidłowej tarczy do cięcia obowiązuje ogólna zasada, że im twardszy jest materiał do cięcia, tym bardziej miękkie powinno być spoiwo stosowanego materiału ściernego. Przyczyna: Decydująca dla trwałości tarczy do cięcia jest informacja, czy powierzchnia cięcia obrabianego przedmiotu twardnieje, czy nie. Wysoka temperatura powoduje, że tarcza ulega ?zeszkleniu?, tracąc w ten sposób właściwości tnące. W takim przypadku twardość spoiwa powinna być mniejsza i należy wybrać bardziej miękką tarczę.
Prawidłowe zamocowanie ...
... dla lepszego przeniesienia siły
Tarcze do cięcia i szlifowania mocuje się na maszynie za pomocą kołnierzy mocujących. Dzięki tym elementom następuje przeniesienie sił napędowych na tarczę. Wobec tego ze względów bezpieczeństwa bardzo ważne jest, aby nie stosować uszkodzonych kołnierzy mocujących lub nie nadających się do użytku.
... dla większego bezpieczeństwa
Zastosowanie kołnierza mocującego FL 76 gwarantuje zwiększoną stabilność boczną i tym samym bezpieczniejsze prowadzenie tarczy szczególnie dla prostych, cienkich tarcz do cięcia o średnicy od 180 mm do 230 mm. Stosując kołnierz mocujący należy przestrzegać obowiązujących przepisów i norm. Bezwzględnie zgodne muszą być powierzchnia przyłożenia i średnica kołnierza. Zastosowanie kołnierzy mocujących o różnych średnicach jest niedozwolone.
Różnica pomiędzy gwintownikiem a wygniatakiem
W przemyśle występują różne metody wytwarzania gwintów wewnętrznych, najbardziej popularnym jest gwintowanie następnie wygniatanie gwintów i rzadziej stosowane frezowanie.
Gwintowniki oraz wygniataki są to narzędzia przeznaczone do wykonywania gwintów wewnętrznych, różnią się tym, że gwintownik wykonuje gwint metodą wiórową, a wygniatak bezwiórową.
Ta pierwsza polega na oddzieleniu mechanicznym materiału od przedmiotu obrabianego, natomiast druga metoda polega na wygniataniu na zimno gwintu, bez przerywania włókien materiału.
Często spotykamy się z pytaniem co wybrać gwintownik czy wygniatak ?
Gwintowniki są narzędziami wieloostrzowymi przeznaczonymi do nacinania gwintów w otworach.
Gwintowniki można podzielić na wiele typów, zależy od rodzaju nacinanego gwintu: do gwintów walcowych i stożkowych, do gwintów metrycznych, calowych, trapezowych, rurowych itp.
Zalety gwintowników:
- uniwersalne zastosowanie w maszynach CNC, maszynach konwencjonalnych jak i przy zastosowaniu pokręteł ręcznych bez konieczności zasilania energią elektryczną.
- możliwe jest stosowanie gwintowników w materiałach utwardzonych.
- gwintownik precyzyjnie nacina profil gwintu.
Wygniataki (gniotowniki, gwintowniki bezwiórowe) przeznaczone są obróbki materiałów o dobrej odkształcalności. Do takich materiałów możemy zaliczyć aluminium i jego stopy, metale kolorowe, stale nierdzewne, kwasoodporne oraz zwykłe stale konstrukcyjne.
Zalety w porównaniu do gwintowników:
-Wygniatanie gwintu trwa zwykle krócej od jego skrawania
-Możliwość wykonywania głębokich gwintów, do 3.5 × D, bez problemów z odprowadzaniem wiórów
-Zazwyczaj trwalsze od gwintowników
-Jeden typ narzędzia może zazwyczaj pracować w różnych materiałach, jak też w otworach przelotowych i nieprzelotowych
-Stabilna konstrukcja, małe ryzyko złamania narzędzia
-Gwarancja wykonania gwintów o żądanych tolerancjach
-Nie generują wiórów
-Wytrzymałość gwintu większa nawet o 100% (większa wytrzymałość na ścinanie)
-Mniejsza chropowatość powierzchni gwintu.
Płytki wieloostrzowe i narzędzia składane do obróbki skrawaniem
Skrawtech oferuje szeroką gamę płytek wieloostrzowych z węglików spiekanych. Stosowane gatunki węglika, nowoczesne powłoki super twarde i geometria ostrza skrawającego pozwalają na prowadzenie wydajnej i efektywnej obróbki wykańczającej, średnio dokładnej i zgrubnej stali węglowych, stopowych, nierdzewnych, żeliw oraz metali nieżelaznych.
Węgliki spiekane:
-Gatunki węglików spiekanych
-Tabela zbiorcza gatunków do toczenia
-Oznaczenie płytek do toczenia
Narzędzia do toczenia:
-Oznaczenie noży do toczenia zewnętrznego
-Oznaczenie noży do toczenia wewnętrznego
-Noże do toczenia zewnętrznego
-Noże do toczenia wewnętrznego
-Przecinaki listwowe
Narzędzia tokarskie na płytki wymienne
To wszystko zawiera katalog firmy YG-1, której przedstawicielem jest Skrawtech
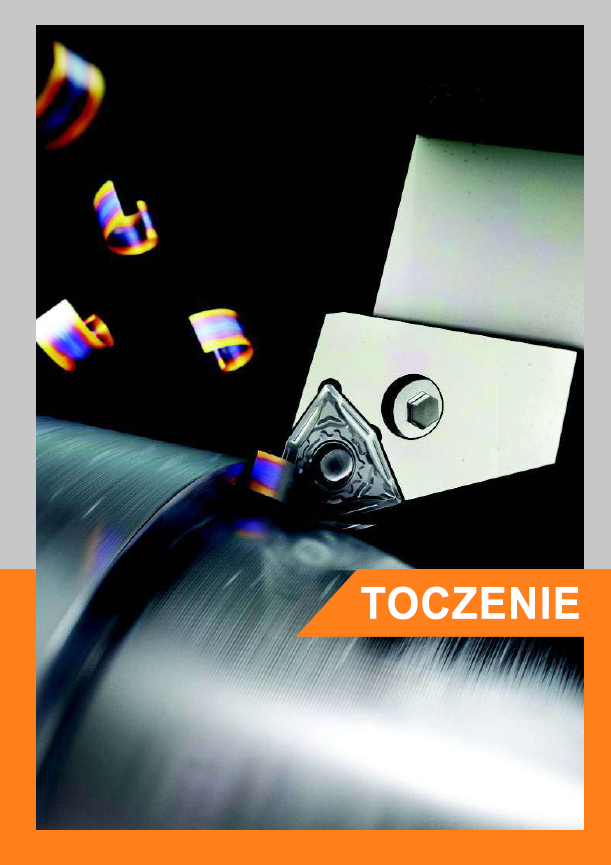
Szukasz gwintowników do zastosowań uniwersalnych, proponujemy:
COMBO TAPS
- Wykonują gwinty M, MF, UNC, UNF w tolerancjach -6H, -4H, -6H+0,1, -6G, -7G, -2B, -3B.
- Produkowane są z luka wiórową skrętną do otworów nie przelotowych, lub ze skośną powierzchnią natarcia do otworów przelotowych.
- Stosowane na maszynach numeryczne CNC, lub na starszych maszynach konwencjonalnych.
Dodatkowe wykonania gwintowników COMBO posiadają :
- Wewnętrzny układ doprowadzenia chłodzenia do przestrzeni obróbczej IKZ.
- Wydłużoną część chwytową podobnie jak gwintownik NGMf.
- Opatentowaną przez YG-1 geometria gwintowników COMBO zapobiega rozbijaniu gwintu w otworze, gdy stosujemy zbyt duże posuwy.
- Wykonania wg. norm DIN 371, DIN 376, lub DIN 374, ze stali szybkotnącej HSSE, lub ze stali proszkowej HSS-PM.
- Z powłoką TiN, lub Vap, lub bez powłoki.